Brush Plating
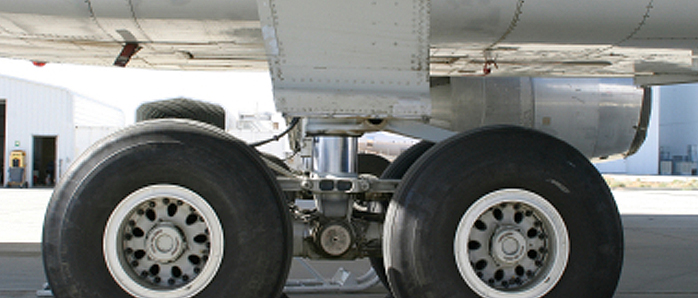
The mechanics of Brush Plating are actually quite simple. A 110 volt AC power pack converts the voltage into DC current. There is a ground cable (negative charge) connected to the part which makes it the cathode. The second cable is (positive charge) connected to the plating tool which makes it the (anode). The anode is wrapped in an absorbent material which holds the plating solution between the anode and the cathode. The electrical current travels from the anode tool through the specially formulated plating solution to the work area. Plating occurs only where the tool contacts the work-piece. Little to no heat is generated throughout the plating process, therefore no internal stress or heat distortions are imparted to the work-piece. The metal deposits are dense, hard, extremely corrosion resistant and metallurgically sound.
There are a wide range of build-up and alloyed plating materials available, contact us to determine what is right for you.
A closely-related process is brush electroplating. In this process entire objects, or sometimes localized areas of items are plated using a brush saturated with a plating solution. The brush, typically made of stainless steel wrapped with a cloth material that holds the plating solution as well as prevents direct contact with the item being plated, is connected to the positive side of a low voltage direct-current power source, and the item to be plated connected to the negative. After dipping the brush in the plating solution, it is moved continually over the surface of the object to achieve an even distribution of the plating material. The brush as the anode, typically does not contribute any plating material.
Brush electroplating has several advantages over tank plating, including portability, ability to plate items that for some reason cannot be tank plated (one application was the plating of portions of very large decorative support columns in a building restoration), low or no masking requirements, and comparatively low plating solution volume requirements. Disadvantages compared to tank plating can include greater operator involvement (tank plating can frequently be done with minimal attention), and inability to achieve as great a plate thickness.
Reference Wikipedia